As I mentioned in another post, I'm a novice when it comes to quilting. My first baby quilt was a disaster, but I gave it as a gift anyway (with all of the qualifiers). The recipient was delighted (so my daughter says, and her note to me says), and it did not seem to be feigned delight. I showed it to my daughter to ensure that she would not be embarrassed.She has a great eye, and she approved.
With all my trials and tribulations on that quilt, I learned that I needed to learn more. Being able to sew and being adept at basic quilting is not the same thing. I read everything that I could, and with my next attempt, I had very good results. To wit:
- Cutting: I've employed the double-ruler method to cut. I use one ruler on the right to ensure that my long Olfa lipped ruler is perfectly straight. Even though it has a lip, it is a wee-bit wonky at times. This method gives me perfect confidence that my cuts are straight and sure. No cutting and turning fabric for me. I'm just moving both rulers right to left. And Donna Jordan's trick of putting a 5lb weight at the end of the ruler to stabilize is golden advice. Just get a weight with a hexagonish end. Otherwise the weight will roll places you don't want it to. Yes, there are other ways that very excellent teachers espouse--I found my way, and it works perfectly for me.
- Piecing: If you've cut it right and pressed your blocks right, then it ought to go together right. In theory. Donna Poster has great video series. The greatest tip (to my eye) was easing seams. Specifically, holding the each point of your piecing firmly and letting the machine ease the difference. Now, too much easing will cause puckers, etc, but a little will ensure that things align as they 'should.' In 'regular' sewing, easing is an important skill...and it takes pracice. But the machine should work for you. But if you have your walking foot on...nope.
- Pressing: I used 2' x 4' rug pad on top of a 2'x4' piece of plywood. I upholstered a linen/cotton fabric to it, and it serves as my pressing board. I had a squishy over the door ironing board fashioned as a tabletop. It was distoring my pieces (which were all bias cuts!!!). I love this board. It sits on top of a low wicker bookcase of the same size
While it is "just that easy," it takes practice...practice builds muscle memory so you are not thinking very minute about what to do right and what wrong to avoid.
I've been purchasing some fabric. My 'never-pay-retail' mentality has led me to two places:
Hancocks of Paducah, and you guessed it, Walmart...oh, and Tuesday Morning. First, the former. Hancocks has lots of fabric on sale. Lots. So if you are new to quilting, why not practice on $4/yd fabric rather than $12? I have bought some really lovely fabric from them at the $3.99 price point. (I also bought some more expensive yardage....). Walmart has love Waverly Inspiration Fat Quarters at .97. That's about $4 a yard too! They are in single packs and include many cute prints. I'm typically dismissive of Walmart...for no good reason. I've also found some really cool fabric at Tuesday Morning. I'm a regular shopper there...but I never noticed they sold fabric until......

I bought a strip set of Ann Rowan's "Sing your Song". I wasn't sure what to make with it. I didn't feel like trying to figure out how to make a quilt with it. When making a sandwhich, I considered my interfolded deli paper. Hmmm...I think that will make an interesting stitching base.
Testing my hypothosis, I took the deli paper (10" x 10.75") which is folded exactly in half. There is a 'slightly waxed' side...and a duller side. It is no where near as waxy as wax paper. So, no concerns for a mess when you get your iron to it.
Cutting along the fold yields two lovely rectangles, the perfect size for a snack mat. Using this method, you are treating the deli paper substrate as your 'foundation'. You can lay your pieces lengthwise, widthwise or on the diagonal. I chose the latter. Stitching to paper means that you can cut your strips any way you please. laying your first strip (however you wish) on the dull side of the paper with the right side of the fabric up. Start anywhere you like on the paper, just ensure that all pieces overlap the paper and your seams extend beyond the edges. Yeah, it is a little bit of fabric waste, but with careful cutting, you have just bits for your leaders/enders in your machine. Also, if you mess up and don't use the dull side, nothing terrible will happen to either your iron or your fabric. It's foolproof and cheap--
With a narrower stich width, this stuff tears off like a charm. What is really great, is that when you are finished your stitching, you already have a square base from which to cut. Just flip over the project, and use your ruler to cut off the excess...lining up your ruler against the paper. It has square corners...just like your ruler--though the edge is a wee bit hard to see given that it is transluscent.
I was SO HAPPY with my results. With the top completed, just cut a backing and some batting the size of your top. Layer
batting
project back with wrong side to batting
project front with right side to back
Stitch (1/4" min) along the outside leaving a space of 4". Mark where you are going to turn...the hum of the machine makes the mind wander and before you know it, your project is completely tucked inside of your perfectly sewn perimeter. Before turning, trim each of your corners.
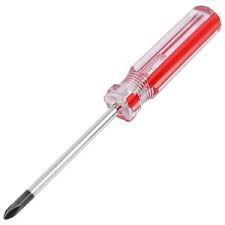
There are lots of ways to turn a project. I happened to have a screw driver handy, and I thought I would take it for a drive. It works great. Let me tell you why. The glass handle (don't use any with a grip), slides easily over your fabric. Unlike other 'methods' of turning, the wide end helps immensely in turning your side seam out. Sometimes they get tucked in...this business end will push them out nicely.
Now, the second business end does a marvelous job of poking your corners out. The picture is of a Phillips head, I have a flat head. Though, I'd be interested to see if one is better than the other. This tool has the added benefit of your not having to stuff your darn and in your project. So use a long screw driver.
 |
Ann Rowan's "Sing your Song" |
After your project is turned, turn in your fabric where you turned your project. Press. Then stitch (bring bobbin thread up first) 1/8" around your project. You can then "stitch in the ditch" along the seams on the face of your project....or machine quilt if you are good at that. I'm still working on being a stitch in the ditch master.
My project turned out beautifully (to my standards). The 1/2 10 x 10.75" deli sheet makes the perfect sized snack mat that is easy to make and will be delightful to use. These mats are a great way to let your friends know that you are thinking about them. And they'll remember you each time they use their mat.
While this piece is backed, you could simply make quilting blocks by cutting in half, OR by using the entire sheet of deli paper it makes a 'squarish' block.
P. S. I found some